Evropski Korejci osvajaju svet
„Čelično srce Češke” je drugo ime za najveći grad u Moravskoj oblasti. Grad Ostrava je preko dva veka poznat kao industrijska zona, okrenut rudarstvu i teškoj industriji, poznat po proizvodnji čelika, a i nama omiljenog proizvoda na četiri točka. Zbog toga ne čudi zašto je južnokorejski gigant odlučio da baš u ovoj oblasti sagradi svoju najveću fabriku u Evropi
Impresivna Hyundaijeva fabrika u Češkoj, godišnje proizvede skoro 360.000 automobila
Motiv da posetimo severoistok Češke bio je ljubazan poziv naših domaćina, ovlašćenog uvoznika za Hyundai vozila, firme Hyundai Srbija. Svrha naše posete, bila je da uživo vidimo kako izgledaju proizvodna postrojenja u kojima se proizvode automobili ove marke, a koje smo već imali priliku da testiramo.
„Hyundai Motor Manufacturing Czech” (HMMC) je najmlađa fabrika automobila u Evropi, a ujedno je jedna od najmodernijih. Sagrađena je u okolini trećeg po veličini grada u Češkoj. Na nekih tridesetak kilometara od grada Ostrave, nalazi se selo Noševice, koje po poslednjem popisu stanovnika broji nepunih hiljadu duša. Ovaj podatak je zanimljiv iz razloga što Hyundaijeva fabrika zapošljava tri puta više ljudi, tačnije blizu tri i po hiljade radnika.
Zašto baš Nošovice?
Nije potrebno puno vremena da se saberu dva i dva, dovoljno je malo „mućnuti“ glavom i odgovor je tu. Pored dobre poslovne klime i povoljnih uslova koje su obezbedile češke vlasti, u prilog ide i lokacija odnosno geografska pozicija Moravske oblasti. Fabrika je praktičko izgrađena u centru Evrope. Na samo 90 kilometara južno od Nošovica, nalazi se sestrinska fabrika Kie u Slovačkoj, u mestu Žilina. Ove dve fabrike su u konstantnoj komunikaciji. Iz Nošovica se šalju menjači za Kijine modele, a iz Žiline pogonske jedinice za Hyundai automobile.
Zanimljiv podatak je da u okviru Hyundai grupe, posluju kompanije koji su lideri u proizvodnji čelika u svetu, što nas dovodi do još jedne dodirne tačke sa pomenutom lokacijom. Takođe, treba uzeti u obzir i tradiciju koju poseduju Česi u proizvodnji automobila. Prvi automobil koji je proizveden u Centralnoj Evropi davne 1897. godine, bio je model „Prasident“, delo fabrike automobila „Nesselsdorfer Wagenbau-Fabriks-Gesellschaft“, nama poznatije kao Tatra.
Kada smo se već dotakli Tatre, pomenimo koliko su talentovani češki inženjeri. Tatra je proizvodila pogonske jedinice za kamione, autobuse, automobile, avione i vozove. U njihovom portfoliju moglo se naći sve, od jednostavnih dvocilindričnih bokser motora sa vazdušnim hlađenjem, pa do pravih, neverovatnih inženjerski remek-dela, motora koji su bili u „W“ konfiguraciji i posedovali čak 18 cilindara
Kako je sve počelo?
Hyundaijeva globalna strategija osvajanja tržišta podrazumevala je i osvajanje evropskog kontinenta. U proleće 2005. godine, Hyundaijev menadžment doneo je odluku gde će izgraditi svoje nove proizvodne pogone. Već u martu 2007. godine, građevinske mašine krenule su u akciju. U rekordnom roku, za nepunih 20 meseci, prema rečima eksperata iz auto industrije, nikla je jedna od najsavremenih fabrika automobila u Evropi.
Rešenost Hyundaija da uzme dobar deo kolača na evropskom tržištu, može se videti i po direktnoj investiciji čija vrednost je premašila 1,120 milijardi evra u startu. Ujedno ovo je najveća direktna investicija u istoriji Češke. Takođe, prilikom izgradnje, južnokorejska kompanija demonstrirala je svoju posvećenost ekološkim principima. Preko hiljadu stabala postojeće šume, nisu bila posečena, već su presađena uz korišćenje najsavremenije tehnologije.

Iako je počela sa radom u najgorem mogućem trenutku, kada je velika ekonomska kriza poput groznice počela da trese automobilsku industriju, kompletna investicija vratila se za svega pet godina. Od otvaranja fabrike, pa do danas, uloženo je dodatnih 400 miliona evra, a prema rečima Hyundaijevih zvaničnika sve se višestruko vratilo.
Treba pomenuti činjenicu, da pored 3.400 radnika koji direktno rade u fabrici, Hyundai je stvorio još 7.000 radnih mesta u proizvodnim pogonima dobavljača.
Fabrika se prostire na površini od 200 hektara, a čine je osam hala, upravna zgrada, test staza, parking prostor za automobile radnika, parking za proizvedene automobile, kao interna železnica, uz pomoć koje se distribuira 40% proizvodnje.
Zanimljivi brojevi i modeli
Već smo pomenuli neke impresivne cifre, ali bi smo se osećali dužni kada Vam ne bi preneli sve što smo čuli na licu mesta. Godišnja proizvodnja Hyundaijeve fabrike iznosi blizu 360.000 automobila i 530.000 menjačkih sklopova. Praktično, svakog minuta sa proizvodne trake siđe po jedan automobil, svakog sata proizvede se 66 automobila, a dnevna proizvodnja je oko 1.500 vozila.
Trenutno u Nošovicama se proizvode tri modela. Hyundai i30 treće generacije, proizvodi se u dve karoserijske izvedbe, karavan i hečbek sa petoro vrata. Krajem godine priključiće mu se Fastback verzija kupea sa četvoro vrata, kao i nabrijana varijanta hot heča i30 N. Najstariji model u portfoliju je mini MPV iz „B” segmenta, model ix20, koji se proizvodi još od 2010.godine. Okosnicu proizvodnje čini naslednik rekordera fabrike, SUV modela ix35. Sa 70% učešća u ukupnom broju proizvedenih automobila, popularni Tucson je glavna uzdanica češke fabrike.
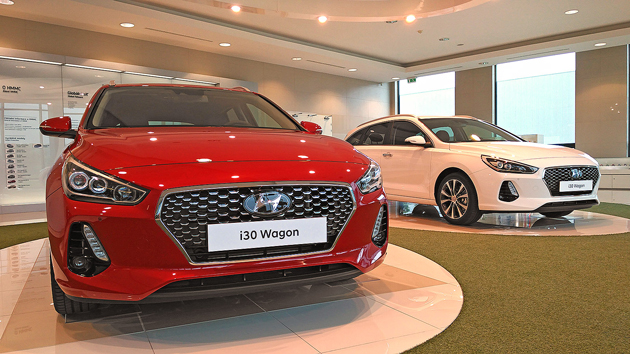
Kroz pet faza do automobila
Figurativno rečeno, pre nego što krenemo u proizvodnju i sklapanje automobila, za trenutak ćemo se vratiti na priču o halama. Od pomenutih osam hala, pet pripada Hyundai Motor Manufacturing Czech i u njima se odvijaju procesi proizvodnje i finalnog sklapanja. Preostale tri hale pripadaju dobavljačima. Hyndai Steel je fizički odvojen od ostalih. U ovaj pogon doprema se čelik direktno iz Južne Koreje, a potom se dodatno obrađuje i namotava u ogromne rolne. Drugi dobavljač je firma Mobis, koja obavlja veliki deo priprema za halu u kojoj se sklapaju vozila. U Mobisu se kompletiraju moduli prednjeg i zadnjeg oslanjanja, kočionog i upravljačkog sistema. Takođe ova firma je zadužena da menjač iz hale pored, bude sjedinjen sa motorom koji je stigao iz Kijine fabrike u Žilinama.
Daymos je treći dobavljač koji se nalazi u Hyundaijevom dvorištu i zadužen je za isporuku sedišta. Transport komponenti između svih sedam hala obavlja se preko mostova koji povezuju hale. Na ovaj način, još jednom je došla do izražaja Hyundaijeva ekološka svest. Umesto stotina kamiona koji bi cirkulisali u krugu fabrike, postavljene su pokretne trake na mostove. Ipak bez kamiona se ne može. Na svaki minut u halu za sklapanje pristigne kamion sa delovima koje proizvode eksterni dobavljači, odnosno oni koji nisu u krugu fabrike.
A sada ono najzanimljivije, korak po korak kroz proizvodne hale. Početak proizvodnje startuje u hali sa presama, hala broj 1. Rolne galvanizovanog čelika razmotavaju se po pokretnoj traci, zatim ih sekači seku, a potom presa oblikuje u neki od karoserijskih panela. Sva tri modela imaju 17 delova karoserije.
U hali broj 2 odvija se proces varenja. Postupak je potpuno automatizovan, preko 300 robota obavlja ovaj delikatan posao. Ljudska radna snaga je skoro isključena iz ovog procesa, faktički samo par kontrolora proverava uzorke. Tokom boravka u ovom pogonu primetio sam nešto zanimljivo. Svi roboti su brendirani kao Hyundai. Znajući za kompaniju Hyundai Heavy Industries, koja proizvodi brodove mašine, velike motore i još po nešto. Usudio sam se da pitam, da li su to baš roboti koje je Hyundai proizveo.
Potvrdan odgovor je usledio sa velikim osmehom na licu. Znači, Hyundai automobili se prave od čelika koji proizvodi Hyundai Steel, a proizvode ih roboti Hyundai Heavy Industiesa. Mora se priznati da je Hyundai grupa jedna izuzetno moćna kompanija.
Posebnu pažnju privlači robot koji vari pod automobila, može se slobodno reći postavlja temelj za novo vozilo. Ovu „sajnsfikšn skarlameriju“ od milošte nazivaju „main bug“ ili ti glavna buba. Univerzalna i ekstremno moćna mašina za varenje, sposobna je da na istoj liniji obrađuje osam različitih modela.
Prelazak u narednu halu, znači da već imamo nešto što liči na automobil i da je vreme da dobije svoj identitet u vidu boje. Farbare su najstrožije čuvana tajna svih proizvođača automobila i pravo je čudo da smo imali privilegiju da budemo provedeni kroz ovo postrojenje. Uglavnom, proces farbanja je jedan od najdužih u nizu. Naravno, nanošenje boje je samo jedna mala stavka. Svaka karoserija mora biti očišćena i zaštićena antikorozivnom masom, zaranjanjem cele školjke u kadu koja je ispunjena specijalnom tečnošću. Po završetku farbanja, lakiranja i sušenja, svaku karoseriju pregledaće tehničari pod jakim svetlom i dati joj zeleno svetlo ukoliko je sve uredu.
Vreme je za veliko finale. Prelazimo u halu broj 5, ovde se sve komponente spajaju i dobijamo njegovo veličanstvo automobil. Najimpresivnija hala od svih, ogromno zdanje, njena veličina je ekvivalentna veličini 16 fudbalskih terena i čak tri hale su povezane sa njom plus već pomenuti kamioni koji na svakih 60 sekundi kucaju na njena vrata.
Sve karoserije prvo se oblažu specijalno dizajniranim plastičnim oblogama, koje ih štite od potencijalnih ogrebotina tokom montaže. Dok pokretne trake lagano jezde i ponekad se na kratko zaustave, vredne i brze ruke muškaraca i žena obavljaju svoj deo posla. Odnos radne snage prema polu je 83% prema 17% u korist muškarca. Džentlmenska raspodela radnih zadataka je još jedna u nizu pozitivnih kritika. Za dame koje rade u pogonima za sklapanje, rezervisani su fizički lakši poslovi, na primer opremanje enterijera i vrata.
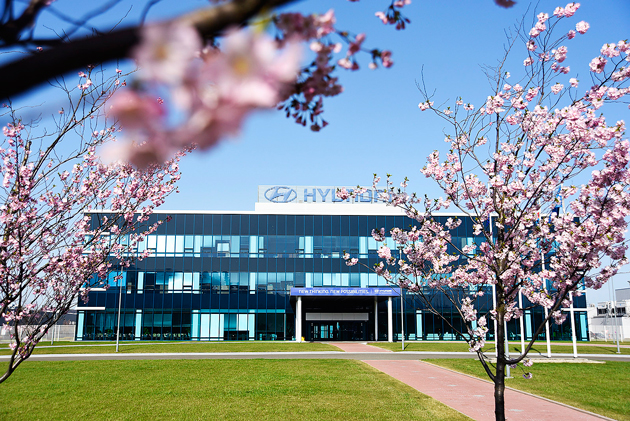
Kada automobil dobije sve potrebne delove, na scenu stupaju test vozači. Prve provere obavljaju se u okviru hale, na mernim instrumentima, a zatim sledi dvanestominutna vožnja na test stazi. Poligon se sastoji iz nekoliko delova, odnosno nekoliko testova, gde se proveravaju upravljački sistem, kočnice, kako reaguje oslanjanje po uzdužnim i poprečnim neravninama. Pored toga, test vozač proverava sve prekidače, svetla, klimu, multimedijski i navigacijski uređaj, kao i sisteme aktivne bezbednosti (ABS, ESP, TC…).
Po završetku vožnje, automobil ide na parking i čeka svoj prevoz do krajne destinacije. Postoje dva vida transporta vozila. Drumskim saobraćajem 60% automobila izađe iz dvorišta fabrike, preostalih 40% prevozi se železnicom.
Najbolje je učiti od uspešnih
Naša poseta Hyundaijevoj fabrici u Nošovicama završila se tamo gde je i počela, u lobiju upravne, administrativne zgrade. Čekajući da krenemo u hotel, po glavi su mi se motale reči našeg domaćina, direktora za odnose sa javnošću, gospodina Petra Vaneka. Pokušaću da parafraziram njegovo izlaganje.
„Važnost Hyundaijeve fabrike u Nošovicama za regionalnu i nacionalnu ekonomiju je ogromna. Regionalno kreiramo preko 10.000 radnih mesta, mi smo šesti po veličini poreski obveznik u Češkoj u kategoriji kompanija koje se bave proizvodnjom.“
Zanimljiv podatak je i to, da 97% radne snage čine Česi iz okolnih mesta. Izvoz je obezbeđen u 66 zemalja sveta, pa se „Češki Korejci“ prodaju širom Evrope, Afrike, Bliskog istoka, Latinske Amerike i Pacifika. Najbolji prodajni rezultati su ostvareni u Nemačkoj, Velikoj Britaniji, Italiji i Španiji.
Pomislio sam, ovako se radi na razvoju nacionalne ekonomije. Vreme je da ozbiljno poradimo na privlačenju velikih investitora. Da uredimo administraciju i da floskula „fali ti još jedan papir“ postane prošlost.
Mudri Petr Vanek, još jednom rečenicom kupio je moju pažnju i pokaza kako profesionalac radi svoj posao. Verujem da će se i Vama dopasti dragi čitaoci.
„Iz naše fabrike još niko nije otišao bez automobila, pa nećete ni Vi. Hvala Vam što ste bili naši gosti.“
Za rastanak svi smo dobili na poklon maketu Hyundai Tucsona.
Iz Nošovica za Vrele Gume: Branko Avramović
Fotografije: Branko Avramović / Hyundai